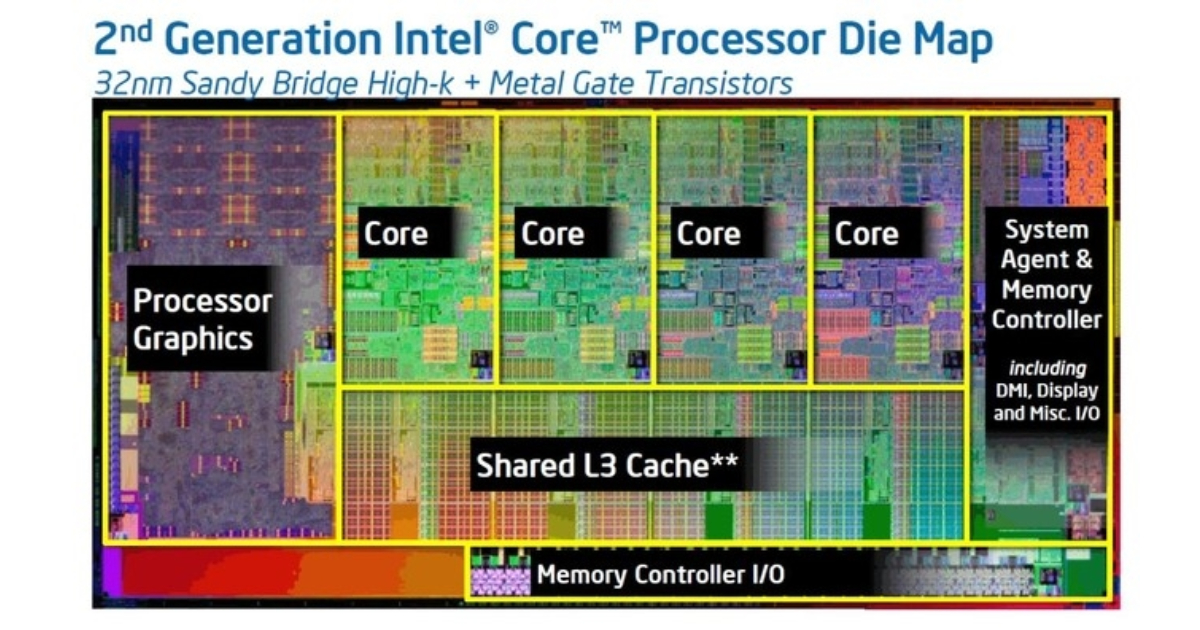
ADVERTISEMENT
談到電腦、手機等硬體的升級,近幾年我們都會用「擠牙膏」來形容新一代產品的性能表現。確實在一年一更新的節奏下,產品的性能提升通常會維持在10%~20%之間,鮮有突破性進展。但每次技術上的躍遷,必象徵著我們的世界又進入了一個嶄新時代。
隨著今年AI在個人使用者中的爆發式增長,不僅伺服器端出現前所未有的超強算力AI GPU加速卡,而且在終端上,電腦的CPU也做到了技術上的全面躍遷,進入AI PC的時代。
CPU早已經不只是CPU
提到CPU,我們的慣性思維,會認為他就是我們電腦的運算核心,我們會非常注重它的性能表現。但實際上,從十年前開始,我們電腦裡的那個「黑疙瘩」,早已不單純地只具有CPU的功能。
早在2011年,Intel 第二代Core處理器(代號Sandy Bridge)就已經將GPU及相關顯示輸出介面電路與CPU晶片內建在一個裸晶上。此外,視訊編解碼器、訊號處理器等各種專用加速單元也被內建入CPU,形成「系統級晶片」,這大幅提升了CPU的處理效率,並減少了對外圍晶片的依賴。
不過,隨著晶片製造的工藝製程向著越來越精細的尺寸迭代升級,在物理特性上越來越逼近現有材料的性能極限,技術實現越來越困難,晶片製造成本急劇增加。為了能夠內建更多電路,同時又能有效控制良率和生產成本,就出現了Chiplet技術。
Chiplet技術是將一個大晶片拆分為多個小晶片(Chiplet),再透過先進封裝內建到一起。相比之下,SoC技術是在一塊晶圓上製造整個系統,而Chiplet可利用不同廠商的製造技術,讓各晶片獨立最佳化再組裝,完美結合性能與成本。被業界視為繼SoC之後,新一代系統級晶片解決方案。
雖然Intel最新的Core Ultra處理器不是第一款採用Chiplet設計的產品,但這次升級,象徵著PC處理器正式進入了一個新的時代。
Core Ultra四芯合一
Intel最新Meteor Lake架構Core Ultra處理器主要內建了四顆不同製程工藝的小晶片,包括Compute Tile、Graphics Tile、SoC Tile和I/O Tile。
其中Compute Tile部分基於EUV技術的Intel 4製程來製造,而Graphics Tile、SoC Tile和I/O Tile則全部由積電代工,採用台積電5nm和6nm製程生產,最後透過Intel Foveros 3D封裝技術將他們連接到一起。
相比歷代的單一製程單一晶圓製造,Intel Core Ultra不僅在核心架構上實現了異構整合,而且首次採用了多源晶圓製造的方式。可以說是Intel 在工藝技術和晶片設計上的雙重突破。
作為全球最大的半導體公司,Intel一直堅持自主可控的晶片工藝技術。早期的摩爾定律推動其處理器性能穩步增長,垂直一體化的封閉生態也成為其支配PC產業的基石。
但是,在晶片製造進10奈米後,Intel工藝技術開始明顯落後競爭對手。曝光機物理極限、介電層難題等障礙大幅拖累其迭代速度。
而TSMC等專注晶圓製造的專業代工廠在7nm/5nm節點上不斷突破。這迫使Intel開始推動策略性轉型,提出了「四年五個製程節點」計畫。即透過在四年內推進Intel 7、Intel 4、Intel 3、Intel 20A和Intel 18A五個製程節點,於2025年重獲製程領先性。
在該計畫的順利推動下,Core Ultra處理器中Compute Tile部分使用了Intel 4製程工藝。同時全新的小晶片設計,在多個製程工藝優勢的協同整合下,為Intel重回製程領先爭取到寶貴的時間。而chiplet模式也預示著半導體產業將呈現跨廠商、跨國界的高度協作與共生格局。
Intel歷代處理器使用的工藝製程和關鍵技術:
- 1971年4004使用10微米PMOS工藝
- 1978年8086使用3微米HMOS工藝
- 1985年80386使用1.5微米HMOS工藝,首次引入32位元
- 1989年80486使用1微米工藝,內建電晶體數突破100萬
- 1993年Pentium使用0.8微米BiCMOS工藝
- 1997年Pentium II使用0.35微米CMOS工藝
- 2000年Pentium III使用0.18微米Coppermine工藝
- 2006年Core 2使用65奈米工藝,高K金屬柵極
- 2011年第2代Core,32奈米工藝,CPU內建GPU
- 2012年第3代Core,22奈米工藝,三柵級FinFET技術
- 2017年第8代Core,14奈米++工藝,Tick工藝節點出現了較大的延遲
- 2019年第10代Core,10奈米、14奈米混用
- 2021年第12代Core,Intel 7(10奈米)工藝,CPU採用性能混合架構,大小核設計
- 2024年Core Ultra,Intel 4(7奈米)工藝,分離式模組化設計,首次採用多源晶圓製造
請注意!留言要自負法律責任,相關案例層出不窮,請慎重發文!